Continuous casting: horizontal, vertical downward, vertical upward
In production of our wares we use one of the most sophisticated method to cast copper alloys – continuous casting. This method of metal casting is most effective, if it is necessary to manufacture semi-finished products of standardized form in large series. This method provides increased control over the process through automation. Equal and continuous supply of metal, its crystallization and removal of the product allows obtaining a homogeneous semi-finished metal product during the casting process. Through the use of intensified cooling with water it is possible to increase the speed of crystallization. Choosing the right speed there can be a focused crystallization in the material (basically lengthwise to the cast axe) achieved and dense bars, semi-finished products and such with a fine structure of crystals and even chemical composition produced.
Continuous casting allows to produce a wide range of different profiles: cylindrical bares, tubes, square bares and tubes, hexagonal profiles, slabs of various thickness and width etc. This method allows achieving any profile form which is possible to flare through the crystallizer.
The advantages of continuous casting
The use of continuous casting gives a range of advantages in comparison to conventional casting in moulds:
- continuous casting is perfect for manufacturing semi-finished products (bars, slabs) of long sizes;
- the microstructure of long semi-finished products is homogeneous and due to this there is less possibility for arising of tension in the product and the finished parts made from such products will be more durable;
- continuous casting reduces metal cuttings and loss of metal compared to casting in moulds;
- continuous casting is more cost-effective regarding the energetic consumption;
- there are less workers needed at the production process compared to casting in moulds;
- all operations can be easily automated and supervised;
- it is easy to modify the quality and features of the semi-finished products by changing the cast parameters (the pulling speed of the product, the temperature of the crystallizer’s water);
- continuous casting allows to manufacture metal slabs or bars in large amounts by short time.
History
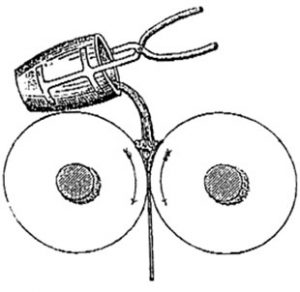
Horizontal continuous casting
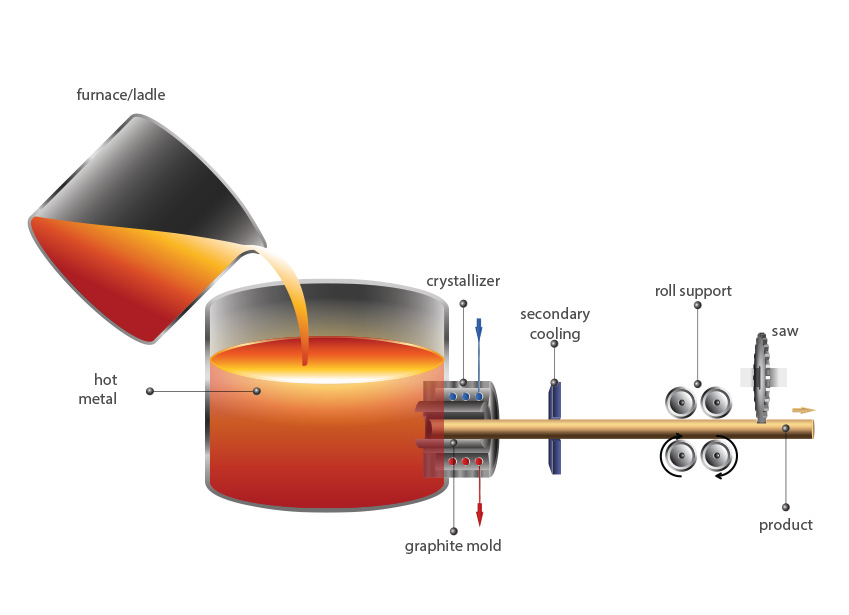
The drawing illustrates the horizontal continuous casting.
The drawing illustrates the vertical downstream casting. The main components are: melting furnace or transportation ladle, casting furnace with tundish, crystalliser with cooling system and installed graphite mould, secondary cooling, roll support and saw.
The equipment functions as follows: first the metal is molten in the melting furnace and tapped into the ladle for transportation to the casting furnace or given directly into the tundish of the casting furnace. From the tundish the hot metal flows under the influence of gravitation trough the graphite mold, installed in the crystallizer horizontally, where metal is being cooled and gains definite form. The roll supports catches up the product and adjusts the casting speed. The Product comes out of the casting machine horizontally. With a moving circular saw the product is being cut into predefined length and after that passed on for further processing.
Vertical downstream casting
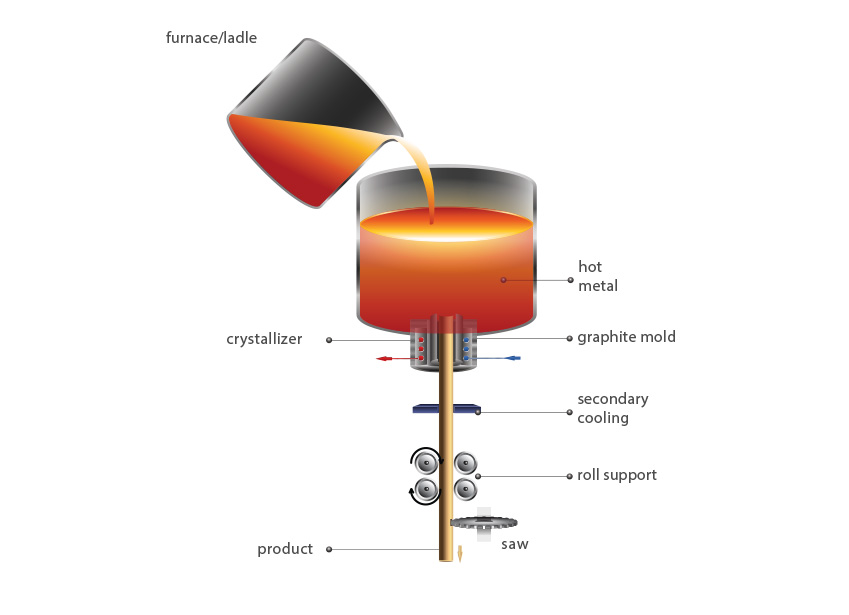
The drawing illustrates the vertical downstream casting. The main components are: melting furnace or transportation ladle, casting furnace with tundish, crystalliser with cooling system and installed graphite mould, secondary cooling, roll support and saw.
The equipment functions are as follows: first the metal is molten in the melting furnace and tapped into the ladle for transportation to the casting furnace or given directly into the tundish of the casting furnace. From the tundish the hot metal flows under the influence of gravitation trough the graphite mold, installed in the crystallizer vertically downwards, where metal is being cooled and gains definite form. The roll support catches up the product and adjusts the casting speed. The Product comes out of the casting machine vertically. With a moving circular saw the product is being cut into predefined length and after that passed on for further processing.
Vertical upstream casting
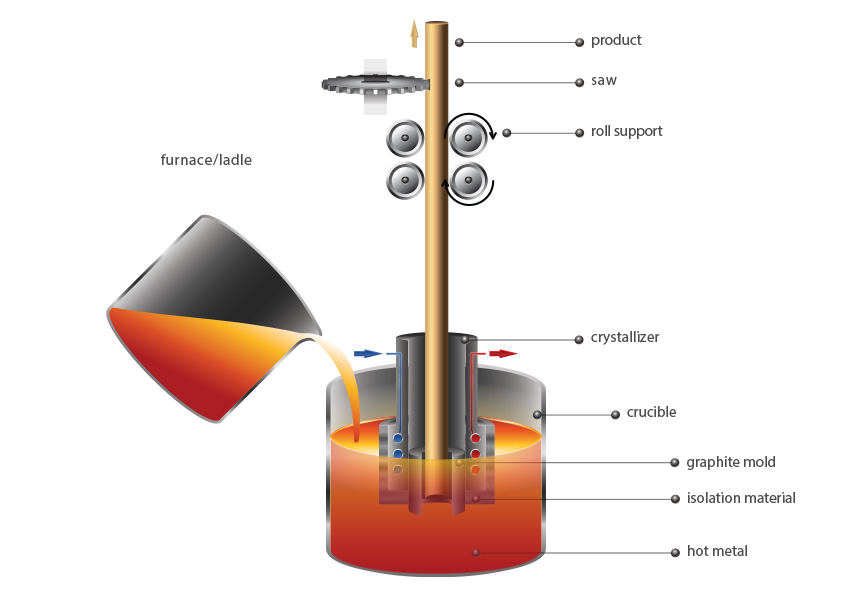
There was equipment for vertical upstream casting for faster manufacturing of thin bars or wires implemented in the 90s of the 20th century. This method is basically being used for manufacturing products of 8-30 mm diameter.
Vertical upstream casting is being used by casting of bronze, copper, nickel alloys, because it has been found out that by casting these alloys vertically up the casting speed is higher and the physical features of the gained alloys are better. The main advantage of this method is the possibility to change the crystallizer fast, to cool it and to warm it up of necessity.
The drawing illustrates the vertical upstream casting. The main components are: melting furnace or transportation ladle, casting furnace with tundish, crystalliser with isolation material, cooling system and installed graphite mould, secondary cooling, roll support and saw.
The equipment functions are as follows: first the metal is molten in the melting furnace and tapped into the ladle for transportation to the casting furnace or given directly into the tundish of the casting furnace. From the tundish the hot metal flows under the influence of interconnected containers trough the graphite mold, installed in the crystallizer vertically upwards, where metal is being cooled and gains definite form. The roll supports catches up the product and adjusts the casting speed. The Product comes out of the casting machine vertically. With a moving circular saw the product is being cut into predefined length and after that passed on for further processing.